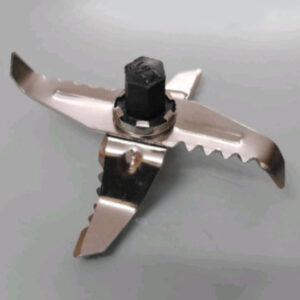
How Mixer Grinder blades are manufactured in industries
How it’s made” sums up the complex and interesting procedures that turn raw resources into final goods. Gaining insight into the production process of commonplace goods allows one to better understand the interplay of science, technology, engineering, and handiwork that defines our environment. This investigation highlights the key phases and methods involved in creating a generic product, demonstrating the painstaking processes from ideation to completion,mixer grinder blades
1. Conceptualization and Planning
The trip starts with a concept, which is frequently motivated by a market opportunity or a need. Designers and engineers brainstorm to conceptualize a product, considering factors such as functionality, aesthetics, and market demand. This phase entails:
Finding consumer requirements, preferences, and trends is known as market research,mixer grinder blades.
Idea Generation
2. Prototyping
Once the concept is solidified, the next step is creating a prototype. Prototyping is crucial as it provides a tangible version of the product for testing and refinement. Techniques used in prototyping include:
-
- 3D Printing: Using digital models to create physical prototypes layer by layer.
-
- CNC Machining: Crafting prototypes from solid materials using computer-controlled tools.
-
- Handcrafting: Skilled artisans may handcraft prototypes for items requiring fine detail and craftsmanship.
3. Material Selection
Choosing the right materials is vital for functionality, durability, and cost-effectiveness. Material selection depends on several factors about ,mixer grinder blades:
-
- Mechanical Properties: Strength, flexibility, and hardness.
-
- Aesthetic Qualities: Appearance, texture, and color.
-
- Sustainability: Environmental impact and recyclability.
-
- Cost: Balancing quality with budget constraints.
4. Production Method
The manufacturing process uses a variety of techniques, each appropriate for a particular kind of product, to convert raw materials into completed goods:
Pouring liquid material into moulds to harden into shapes is known as casting or moulding, and it is frequently used to create metals and polymers.
Machining: The process of utilising equipment such as lathes and mills to cut, drill, and shape materials; frequently applied to metals and hard plastics.
Forming: The process of shaping materials by deformation; mainly applied to metals; includes rolling, extrusion, and forging.
Joining: This process involves joining components together using adhesive bonding, soldering, and welding for a variety of materials.
Additive Manufacturing: Also referred to as 3D printing, this process builds goods layer by layer and is appropriate for intricate and unique designs.
7. Distribution
Once the product is ready, it needs to reach the market. Distribution involves:
-
- Logistics: Managing the movement of goods from the manufacturing site to distribution centers and retailers.
-
- Warehousing: Storing products in warehouses before they are shipped to their final destination.
-
- Transportation: Utilizing various modes of transport, such as trucks, ships, and planes, to deliver products globally.
8. Marketing and Sales
Effective marketing and sales strategies are crucial for the product’s success in the market. This stage includes:
-
- Branding: Creating a strong brand identity that resonates with consumers.
-
- Advertising: Promoting the product through various channels, including digital marketing, print media, and television.
-
- Sales Strategy: Implementing tactics to sell the product, such as pricing strategies, promotions, and partnerships with retailers.
Case Study: The Making of a Smartphone
To illustrate the process, let’s examine how a smartphone is made:
-
- Ideation and Design: Engineers and designers brainstorm features like camera quality, battery life, and screen resolution. They create detailed design blueprints and digital models.
-
- Prototyping: Using 3D printing and CNC machining, they produce prototypes for testing functionality and design aesthetics.
-
- Material Selection: Engineers select materials like aluminum for the body, Gorilla Glass for the screen, and lithium-ion for the battery, considering factors such as durability, weight, and cost.
-
- Manufacturing Process:
-
- Casting and Molding: The phone’s body is often die-cast.
-
- Machining: Precise cuts are made for ports and buttons.
-
- Assembly: Components like the motherboard, battery, and camera are assembled in cleanrooms to prevent contamination.
-
- Manufacturing Process:
-
- Quality Control: Each phone undergoes rigorous testing, including drop tests, battery life tests, and performance benchmarks to ensure it meets quality standards.
-
- Finishing: The phones are polished, screens are coated with protective layers, and software is installed.
-
- Distribution: The finished phones are packaged and shipped to various markets worldwide.
-
- Marketing and Sales: Extensive marketing campaigns highlight new features and improvements. Partnerships with carriers and retailers ensure wide availability.
Conclusion
The making of a product is a complex and multi-faceted process that requires meticulous planning, precise execution, and continuous improvement. From the initial spark of an idea to the final product in the consumer’s hand, each stage plays a crucial role in ensuring the product’s success. Understanding these processes not only gives us a deeper appreciation of the products we use daily but also highlights the ingenuity and effort involved in bringing them to life.
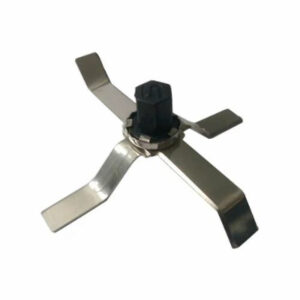